Have you considered using a free punch list template to produce Punch Lists when managing quality control in the close out stages of construction projects?
The manual generation of Punch Lists often incorporates hand written notes transposed into excel spreadsheets which are sorted and emailed to responsible sub-contractors with clumsily attached and poorly referenced photos. This manual re-handle of defect information gives rise to a surprisingly high and often little known cost, borne mostly by the main contractor.
Research led by Professor Marton Marosszeky at the Australian Centre for Construction Innovation (University of NSW) identified the following in respect of the impact of defects:
- On average, the total cost of defect rectification ranges between 4% and 6% of construction expenditure.
- The rectification process is highly management intensive due to the requirement for checking, recording, coordinating, reporting and signing-off reworked activities.
- The indirect management costs are as much as direct rectification costs.
- The administrative cost is substantially borne by head-contractors while the subcontractors bear the direct cost of rework.
In summary, the average cost of defect rectification using traditional methods is 5% with half of this (2.5%) borne by the main contractor in administrative burden.
Consider a $20M construction project; total cost of defect rectification is (on average) $1M with the main contractor’s cost being (on average) $0.5M. This is a significant cost but one that is rarely costed into the closing stages of a project leading to project handover and completion.
Adopting new quality processes is challenging for most construction companies, as usually the change requires embracing new technology and possible unforeseen expenses. Whilst most main contractors claim to encourage innovation, many managers are cautious when it comes to approving expenditures on new construction quality systems, especially when it involves technology they may not be familiar or comfortable with.
Tablet-based defect management systems are widely available but many main contractors are reluctant to implement this time saving technology and persist with manual punch listing processes regardless of the demonstrated productivity benefits and associated cost savings.
We have often speculated the reasons for this and have concluded they most likely are:
- Cost of the new technology/system
- The time/hassle associated with managing change
- Lack of familiarity with the new technology.
This got us thinking of what we could do to overcome these legitimate obstacles.
In our first white paper, we provide you with a free Punch List Template, complete with easy to follow instructions, that will speed up the process of transposing your hand-written notes into a usable Excel Punch List. Given the popularity of and familiarity with Excel, especially in existing manual defect management processes, we considered this the best way forward to give main contractors a taste of the new technology with no cost or risk.
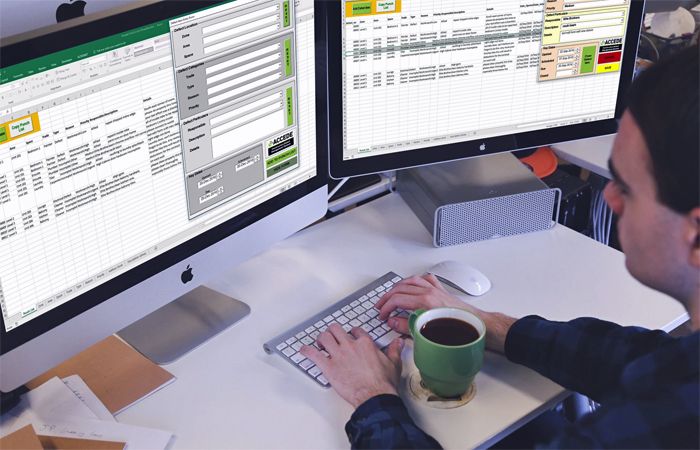
Our solution incorporates Excel-based data entry userforms that:
- contain the key defect item elements you should be capturing
- have a similar look and feel of the ACCEDE Agent (iPad app)
- improve data entry productivity
- generate a simple punch list
- capture data in appropriate formats for direct upload to the ACCEDE Defect Management System should you wish to progress to a free trial
- require minimal change to existing manual punch listing processes.
Unfortunately, our free Punch List Template focuses more on generating rather than managing Punch Lists so the productivity gains from its use are not as great as those you will get from using a tablet-based defect management system. The good news though is it’s free, simple to use and will save time should you wish to proceed with a free trial of ACCEDE.